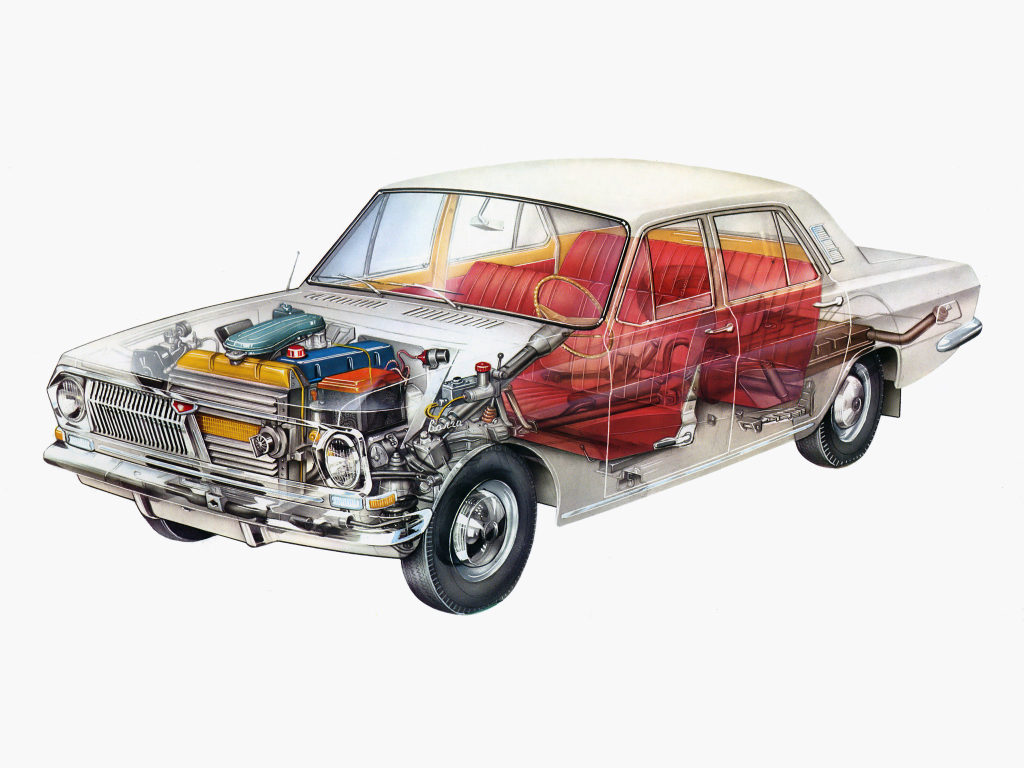
Chassis and body
- All-steel, unitized body and frame
Unlike the previous generation Volga GAZ-21 that was a “partial unibody” car, its front sub-frame bolted to the unibody passenger compartment shell with rubber pads in between, the GAZ-24’s sub-frame is rigidly welded to the floor of the passenger compartment, which greatly improves the body’s structural integrity. Beefy torque boxes connect the sub-frame rails to the body sills, adding even more rigidity and stiffness.
The body was constructed with relatively thick steel and received a phosphate treatment that helped the primer to bond onto the metal and prevented the spreading of underfilm corrosion. Anodic electro-coating was used for evenly applying the primer, and the underbody was treated with a bitumen based undercoating.
However, the inner cavities of the body came from the factory protected by nothing but a layer of electro-coated primer, and in general rust protection didn’t improve much since the days of GAZ-21. In 1970s & 80s, when road salt came to be used much more commonly in winter, it was not sufficient for year-round use of the car in a large city.
That didn’t affect privately owned cars much as they were typically stored in the garage during winter back in the day, and also typically received some additional treatment from the owners making them less prone to rust. However, taxicabs and other state-owned cars, that were used all-year round and usually did not get any additional rustproofing, rusted out in areas such as fenders and door bottoms fairly quickly (usually after 4…5 winters) in the typical climate of central Russia.
Sound insulation was kept to a minimum, both as a cheapening measure and to prevent water collection and rust.
Suspension
- Front: independent, kingpin type; drop-forged unequal-length A-shaped lateral control arms, coil springs, tubular shock absorbers
- Assembled on a separate drop-forged cross-member that holds the control arms and springs
- Rear: longitudinal semi-elliptic leaf springs, live axle, tubular shock absorbers
- Tires: 7.35-14″, bias-ply
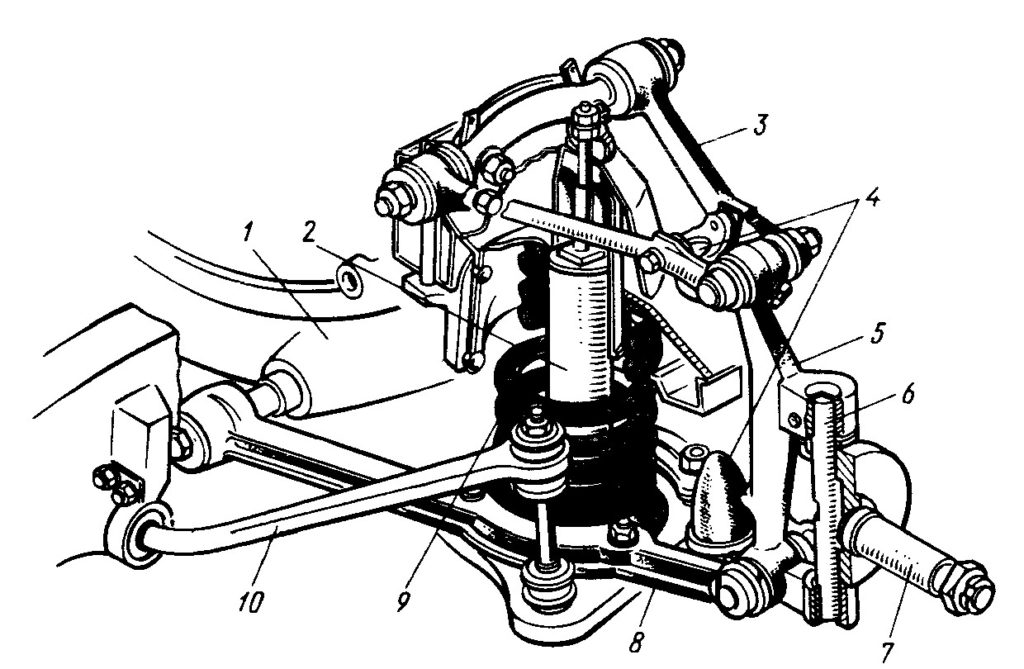
The Volga’s kingpin-type front suspension is arguably one of the most polarizing aspects of this car, receiving love and hate in roughly equal measure. Some people hold it in extremely high esteem for its ruggedness and ability to withstand all kinds of abuse, whilst almost as many tirelessly criticize its for its complexity, laborious maintenance, complicated rebuild procedure and relatively poor handling characteristics. In any case, GAZ was extremely stubborn in its dedication to this type of suspension, using it until early 2000s (albeit with a lot of improvements).
Instead of conventional ball joints, it uses trunnions to connect the A-arms to the spindles. Inner A-arm bushings are rubber, and outer ones are the old-school threaded bushings that need to be lubricated constantly – just as the kingpins (they have tried out rubber for the outer bushings at the development stage, and found out that it just doesn’t work). The advantage is that, unlike ball joints, which can pop out of their sockets if sufficiently worn, trunnions & threaded bushings are virtually indestructible.
Suspension geometry was optimized for longer tire life, which was a serious requirement in the good old days of bias-ply tires, not handling, and the chassis overall has a lot of understeer designed into it. Caster angle is set at zero degrees for lighter steering, as apparently high-speed stability was not the first priority either, so a bit of wandering on the straights is not unheard of (that was fixed in early 1980s in the GAZ-3102 Volga suspension, which had the same design in general, but much better geometry; however, GAZ-24 never received the upgrade). Overall, it is a safe enough handling setup, if you know and respect its limits.
The latest Volga models built after 2003 received a “kingpin-less” ball joint front suspension, which is a great improvement over the old kingpin type. The suspension itself is a simple bolt-on upgrade for GAZ-24, but it requires modifying the steering as well (only replacing the outer tie rod ends, if you are lucky enough to find the version of this suspension designed to work without power steering – which is, unfortunately, the most rare one; or at least the steering knuckle arms from such a suspension). It also employs a different bolt pattern (5×108 mm instead of 5×139.7), so the original wheels will no longer fit.
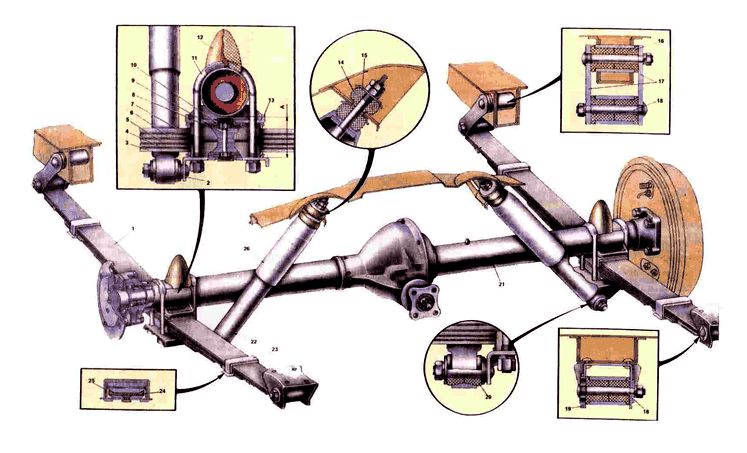
Rear suspension is by leaf springs, and of such a generic design that there is no need for any detailed descriptions.
The original eye bushings were just pieces of rubber held in place by friction and axial compression. Today, modern steel-encased bushing are available for the Volga suspension, as well as aftermarket polyurethane bushings.
Steering
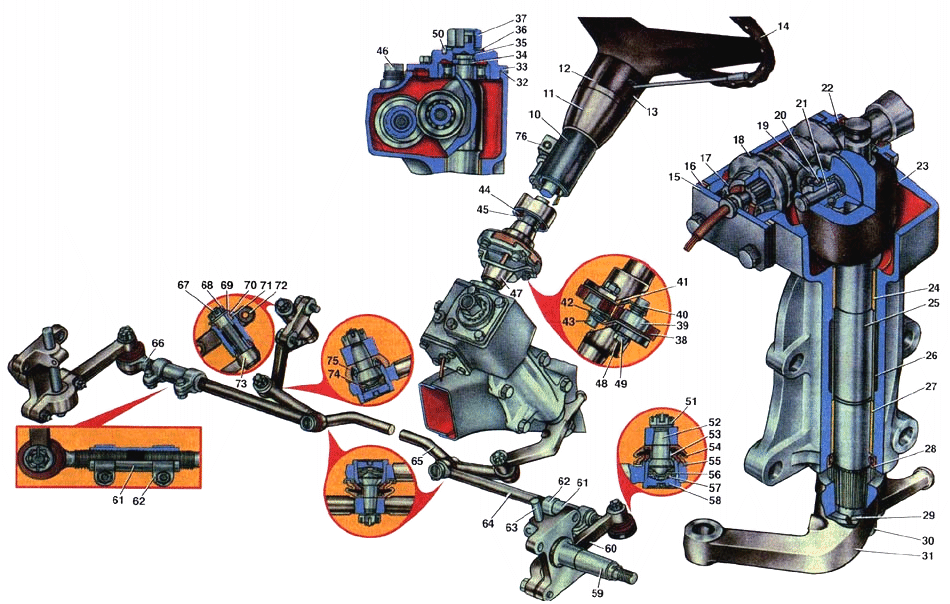
- Worm-and-roller type, manual – except for the V8-powered cars, which were equipped with power steering; the standard manual steering box was retained, and the power assist came from a separate power cylinder assembly attached to the steering linkage
- 19:1 ratio, 4.5 turns lock-to-lock
- Collapsible steering column with rag joint (after 1973)
The Volga’s steering system was designed as a compromise between two tasks: reducing the driver’s efforts required when turning the steering wheel without the use of a power assist, and providing him with effective means to change the course of the car. With a relatively light engine that didn’t put much weight over the front wheels and skinny bias-ply tires, the effort on the steering wheel was indeed quite adequate (comparable to light-class cars).
With fat modern radial tires that no longer works, and power steering becomes a much needed upgrade.
The price, however, was a very “slow” steering ratio, and, as the result, a lot of turns lock-to-lock – which was not a significant problem, as the Volga’s chassis overall was very far from being “sporty”. The large (430 mm in diameter) steering wheel, necessary to increase leverage to turn the wheels, however, may become an issue for the taller drivers.
The front wheels can turn on generous angles (41…43° for the inner wheel in a turn, 35…37° for the outer), resulting in a surprisingly tight turning radius for a car of this size.
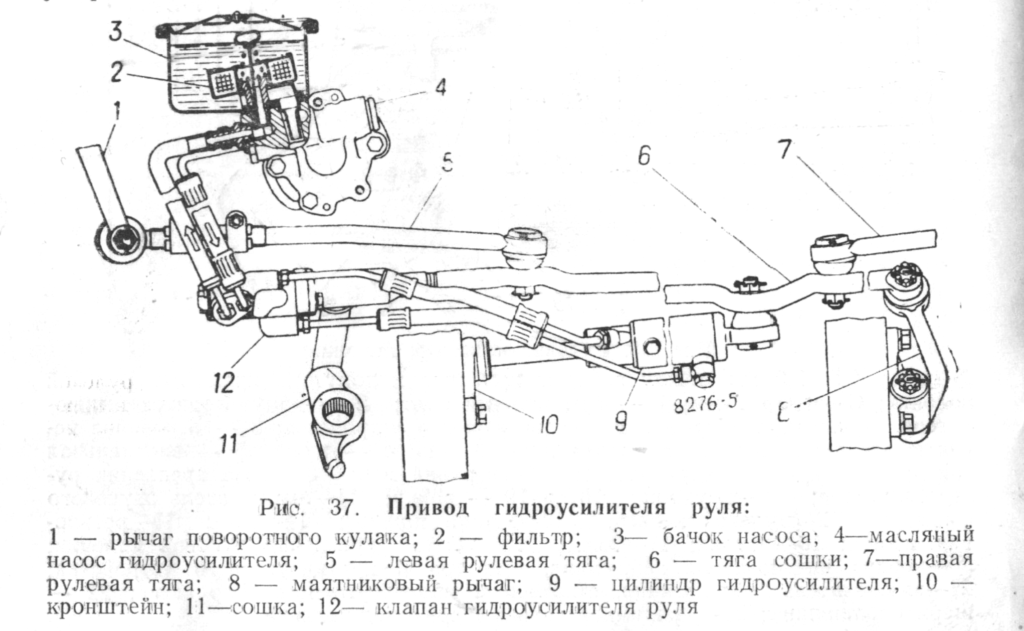
V8 powered cars came with power steering as standard equipment, which was of the linkage assist type, with and external power cylinder mounted to the central link of the steering linkage. It is overall similar to many old Ford & GM designs, such as the one used on C2/C3 Corvette. Just like those systems, is known to be sloppy and leaky, and requires periodic control valve adjustment for proper functioning. It does work, but just doesn’t feel “right” compared to the proper integral power-steering.
At least some cars with power steering are said to have a different steering box (supposedly derived from the Chayka GAZ-13), with a lower gear ratio of 18.2:1 – hence, a somewhat “quicker” steering.
A modern steering box with a built-in power assist is available today for the Volga, but the original GAZ-24 steering column has to be replaced or significantly modified to properly install it. Other modifications may be needed as well.
Brakes
- Front: 11″ duplex (two leading shoe) drum brakes
- Rear: 11″ drum brakes
- Dual-circuit hydraulic system
- Remote hydro-vacuum power assist (Hydrovac)
- Castor-oil brake fluid was originally used
GAZ-24 Volga’s braking system is in fact not a “true” dual-circuit system in the modern sense of these words (with a tandem master cylinder). There is only one master cylinder with one piston, and the two separate circuits are implemented by means of a hydraulic device called the brakes distribution switch, or simply “splitter”:
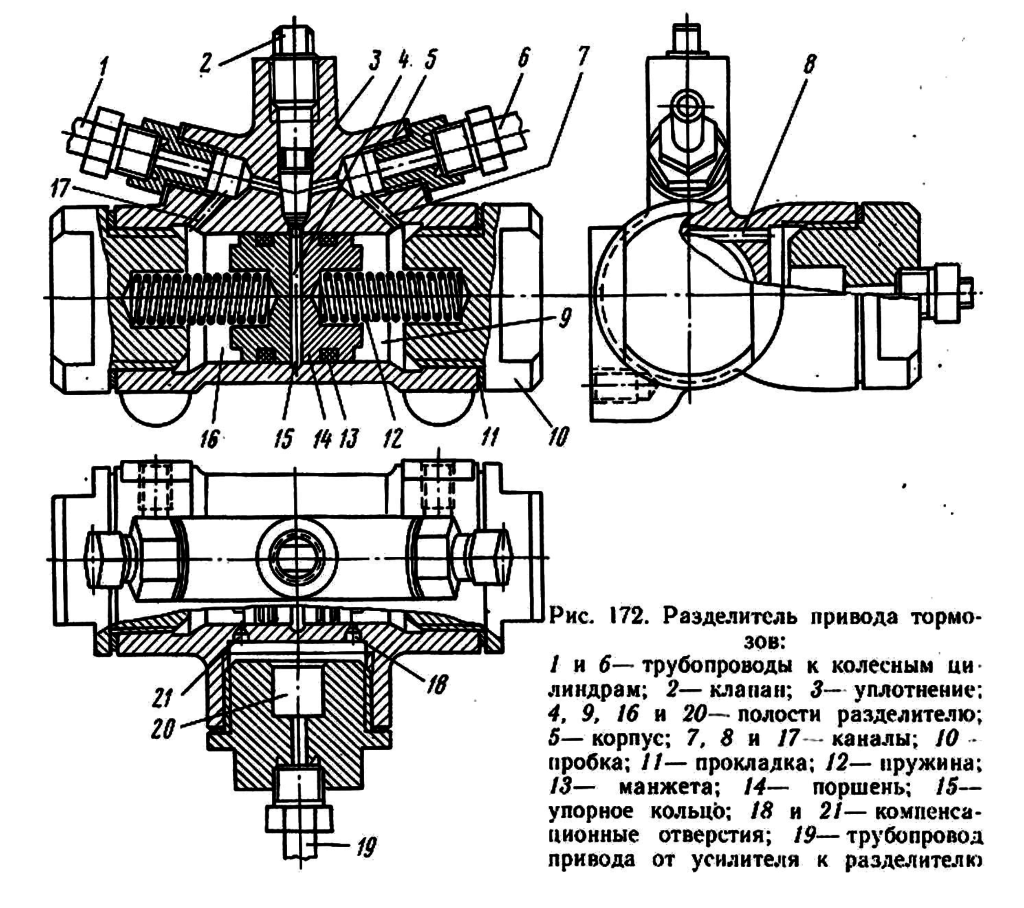
The “splitter” is effectively just a 3-way T-fitting, but it also has two pistons built into it that control the flow of fluid. Hydraulic pressure in the system is transmitted not directly, but through the movement of these pistons.
In normal operation, brake fluid under pressure from the power assist enters chamber 20 and pushes on the pistons, causing them to move off-center. The pistons create equal hydraulic pressure in chambers 9 and 16, which is transmitted to the wheel cylinders. As soon as the pedal is released, the pistons return into central position, and the pressure is relieved.
If one of the circuits (front or rear) springs a leak, during the next braking the corresponding spring-loaded piston inside the “splitter” goes off-center all the way because of the pressure differential – and stays off-center when the pedal is released, cutting off the circuit from the system and preventing further loss of brake fluid (most of the times). A dashboard control lamp goes on at this moment, telling the driver that he no longer has front or rear brakes and has to be very careful, because the stopping distance is now roughly twice the normal stopping distance.
Naturally, the only sane course of actions in this case is to get to a repair facility, soon. From this moment on, the braking system is effectively single-circuit, and if the remaining circuit springs a leak – you will loose brakes completely. Some drivers were so afraid of this possibility that they removed the “splitter” and replaced it with a normal T-fitting, opting for a single-circuit system, which was seen by them as more reliable.
All that said, this system was still a distinct improvement over the older type single-circuit design.
This fundamental design flaw, as well as the front drum brakes that were inadequate for stopping the relatively heavy car from high speeds, were the major problems of the Volga’s braking system. They were addressed in early 1980s when the updated GAZ-3102 Volga came into production. This model got a completely new braking system, with front disk brakes, a conventional vacuum booster instead of the Hydrovac and two completely separate circuits. GAZ-24-10 received most of these upgrades as well, but unfortunately not the disk brakes.
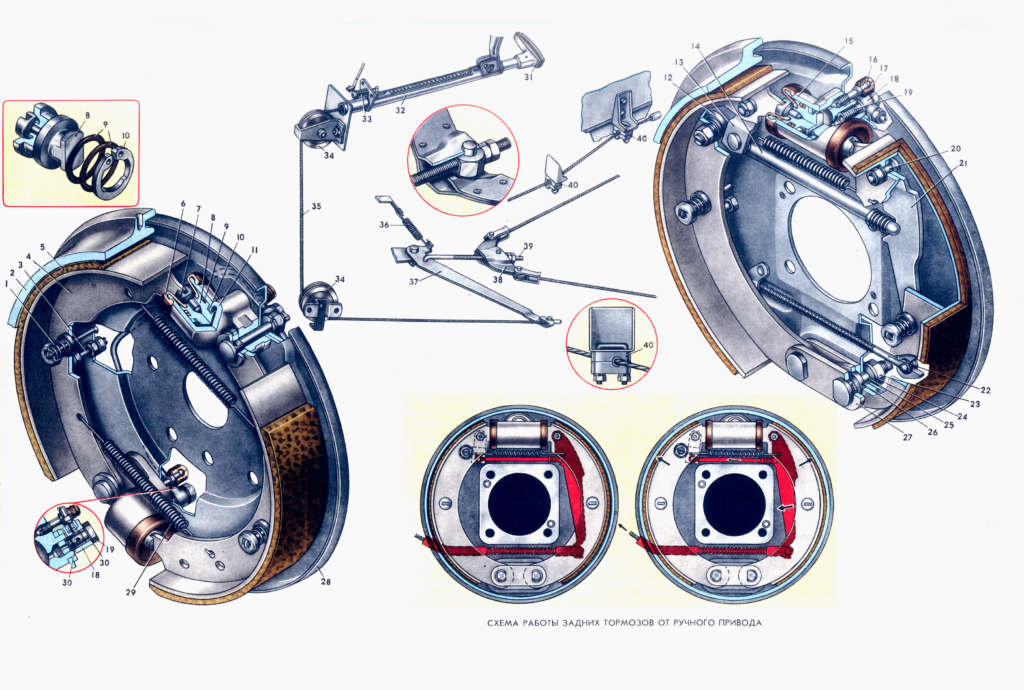
Another somewhat unusual feature of the Volga’s braking system is the use of pinned type of brake shoes, instead of the newer and more common floating (sliding) type. That means that each brake shoe is pivoting around an anchor pin mounted on the backing plate. The anchor pins are eccentric, and must be adjusted every time you replace the shoes to ensure proper functioning of the brakes, which makes the process somewhat fiddly compared to the more common floating-shoe design, in which the shoes have some degree of self-aligning and no adjustment is usually needed.
Chrysler manuals for cars equipped with Chrysler-Lockheed type drum brakes can be used for this adjustment.
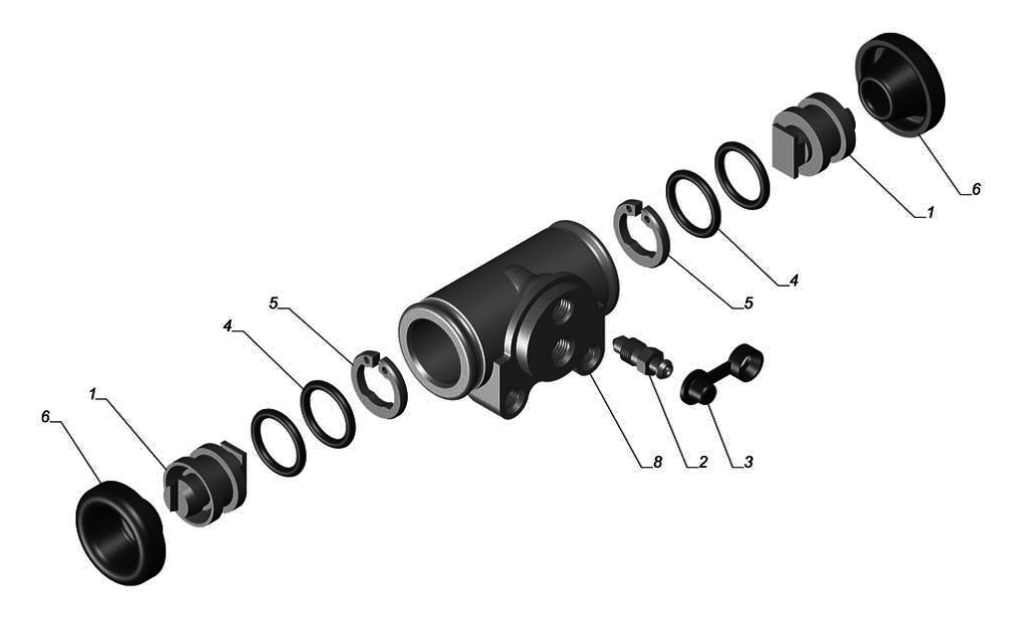
Wheel cylinders are self-adjusting, which means that the limit of movement of the piston is automatically adjusted in response to changes in the shoe gap of the brake, making manual adjustment unnecessary. The ingenious self-adjusting mechanism is very simple and reliable; all of its parts (which there are a few of) are completely contained inside the wheel cylinder.
On early production cars, brake drums were made of a combination of cast iron and pressed steel; late drums, as well as modern replacement parts, are completely made of cast iron. The nominal inner diameter of the drums is 280 mm (roughly 11″) – which is massive for a car of this size and horsepower.